Using built-in system fault diagnosis for motor driven ICs to reduce magnetic field echoes
Time:2023-09-21
Views:673
BridgeSwitch combines efficiency, design flexibility, enhanced security, IEC 60335-1 and IEC 60730-1 compliance, and fault diagnosis capabilities. Designers are facing increasing challenges brought about by the requirement of continuously improving the efficiency and reliability of motor drive in consumer appliances. From the European Union to China, more and more consumer appliances require higher efficiency, including dishwashers, refrigerators, and heating, ventilation, and air conditioning (HVAC) systems. The 1,2 design also needs to comply with the safety requirements of IEC 60335-1 and IEC 60730-1. At the same time, consumers and manufacturers demand higher levels of reliability - fewer on-site services and fewer returns. According to a recent industry study, misdiagnosis leads to 30% of compressor returns being ‘undetected‘, which increases the cost and efficiency of the entire supply chain and leads to consumer dissatisfaction. The use of the Internet of Things can achieve remote monitoring of consumer appliances, but the design must support meaningful and cost-effective fault diagnosis systems and protection functions. To address these challenges, designers can adopt Power Integrations‘ BridgeSwitch series high-voltage self powered half bridge motor driver ICs with integrated protection, system monitoring, and functionality, which can improve efficiency, enhance design flexibility, and enhance inverter and system reliability (Figure 1).
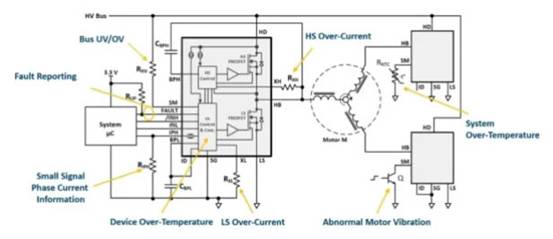
Figure 1- BridgeSwitch combines high efficiency with extensive fault monitoring and (blue text) to improve system and inverter reliability
High efficiency simplifies thermal management of motor drives
BridgeSwitch integrated half bridge simplifies the development and production of high-voltage, inverter driven, single-phase or three-phase permanent magnet or brushless DC motor drivers. The BridgeSwitch IC includes a proprietary instantaneous phase current output signal, which facilitates the design of sensorless control schemes. These ICs include two 600V, N-channel power FREDFETs with high and low side drivers in a small form factor, surface mount package (13.6 × nine point four × 1.35 mm), which can provide longer creepage distance and allow for cooling of both FREDFETs powered by printed circuit boards.
The ultra soft and ultra fast diodes in FREDFET have been optimized for hard switching inverter drives. The high and low side controls and drivers are self powered and do not require external auxiliary power supply. The combination of distributed thermal footprint and up to 99.2% efficiency eliminates the need for external heat sinks at rated continuous RMS current, thereby reducing system cost, size, and weight. BridgeSwitch IC can provide an output power of up to 400 W, making it ideal for inverters in appliances such as dishwashers and refrigerators, as well as condenser fans for efficient air conditioning.
Hardware based fault protection saves costs and time
Most inverter designs use microcontrollers (MCUs) to monitor and respond to fault conditions, as well as control motor drives. Implementing motor drive control using standard software packages is very simple and relatively fast. Fault diagnosis and protection are more challenging, and there may be significant differences from one application to another, as they rely on various sensors to monitor phase currents, system overheating conditions, vibrations, and other system parameters. Programming an MCU to interpret sensor inputs and implement protection in an appropriate manner to achieve international standards is complex. Monitoring software is a time-consuming and costly process that typically delays time to market. On the other hand, the hardware based motor drive fault protection in BridgeSwitch IC meets the abnormal motor drive operation requirements of IEC 60335-1 and IEC 60730-1, eliminating the need for software control, thereby reducing costs and accelerating time to market. Using Class A software that complies with IEC 60730-1 can save two months of time, and using BridgeSwitch IC also simplifies the security approval process for product software updates. BridgeSwitch combines comprehensive internal fault protection functions with external system level monitoring through a bidirectional fault bus (Figure 3). Internal fault protection includes two-stage thermal overload protection for two FREDFETs and hardware programmable cycle by cycle overcurrent protection.
Disclaimer: This article is transferred from other platforms and does not represent the views and positions of this site. If there is any infringement or objection, please contact us to delete it. thank you! |