BLDC FOC Brushless Motor Solution
Time:2024-01-19
Views:367
A typical BLDC/FOC brushless motor solution typically consists of four parts:
There is also a way to integrate all three parts and create a SoC that directly drives BLDC.
01 Motor controller: usually responsible for motor control and algorithm processing by MCU, DSP and other main control chips, and responding to feedback signals from BLDC motors to provide 6 PWM signals for gate drive.
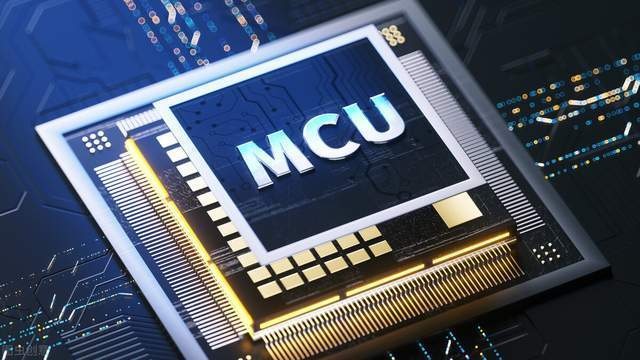
02 Gate drive: also known as "pre drive", it applies voltage to the gate of the power device and provides driving current based on the output signal of the controller.
03 power level: It includes power devices such as MOSFETs or IGBTs, and controls the power output to the BLDC load through switch action, driving the motor to move.
04 Feedback loop: The speed, position, current, voltage, and fault signals of the BLDC motor are fed back to the controller to form a closed-loop control.
The most traditional and mature driving solution is that the controller, gate drive, and power stage are separated; There are also those that integrate gate drivers and power MOSFETs into IPMs.
The current mainstream solution is to integrate gate drive into the controller, and then connect power MOSFET or IGBT to drive BLDC.

MCU+pre drive+drive mode,The advantages of this approach are flexibility, high IC selectivity, and adaptability to various types of large, medium, and small power controllers. It also has the most advantage for general MCU companies, mainly used in high-voltage systems or high-power systems, because high-power and high-voltage applications have issues with heat dissipation and isolation. The disadvantage is low integration, and the area of PCBA is relatively large.
MCU+[pre drive+drive]It can also be described as MCU+IPM. Most international manufacturers developing power components have IPM products, which can simplify the complexity of circuit board design and improve stability for customers. It is also an early and particularly mature driving method. Its advantages are high integration and small PCBA area. The disadvantage is that the power cannot be very high.
[MCU+pre drive]+driver,It is currently a mainstream development direction. Its advantages are high integration, flexible selection of MOSFETs, and suitability for various small and medium power controllers. The disadvantage is that due to the integration of pre drive in MCU, the driving ability and voltage resistance of pre drive are not high, making it unable to adapt to high-power controllers.
SoC method The advantage of it is that it is often used in the design of plastic sealed motors for applications with relatively high performance; The disadvantage is that the design flexibility is relatively poor. If it is necessary to change the driving characteristics, a small MCU must be added next to the SoC. This not only increases the cost of components, but also increases the complexity of the circuit board, which goes against the development concept of simplifying complexity.
There are currently many BLDC motor control manufacturers, and according to different classifications, some companies have all three control solutions, while others only provide one or two solutions.
For example, TI basically has three solutions, and ST also has single MCU and MCU+pre drive methods. The main direction of BLDC control solutions in China is still towards integration, for example, Fengtian mainly provides MCU+pre drive solutions.
From a hardware perspective,The development of BLDC motor control has gone through a process from small-scale analog and digital circuits to separate device controllers, to specialized integrated control circuit controllers, and then to MCU, DSP and other solutions.
From the perspective of software algorithms,Due to limitations in control theory and control devices, BLDC motors have always adopted classical PID control, which can meet various static and dynamic performance requirements. However, the robustness of the system is not satisfactory.
In the face of increasingly complex control objects, to further improve the fast response, stability, and robustness of BLDC motor speed control systems, intelligent control algorithms have attracted attention, including fuzzy control, neural network control, expert systems, etc.
Intelligent control systems have functions such as self-learning, adaptation, and self-organization, which can solve model uncertainty problems, nonlinear control problems, and other complex problems.
The BLDC motor is a multivariable, nonlinear, and strongly coupled control object, so using intelligent control can achieve satisfactory control results. At present, some mature intelligent control methods have been applied to BLDC motor control.
For example, Fuzzy-PID control combining fuzzy control and PID, composite control combining fuzzy control and neural network, fuzzy control optimizing membership parameters through genetic algorithm, single neuron adaptive control, and so on.
Disclaimer: This article is transferred from other platforms and does not represent the views and positions of this site. If there is any infringement or objection, please contact us to delete it. thank you! |