IC troubleshooting and fault analysis
Time:2023-11-01
Views:669
IC fault analysis requires fast and accurate response, as of course, helping customers is our main focus. But should we expect the Quality Assurance (QA) department to test every parameter under all conditions during Fault Analysis (FA)? Not at all. Too much of it is speculation. This may surprise some people, but QA personnel do not have crystal balls or mind reading skills. Only when customers provide accurate technical information about IC faults can IC troubleshooting be carried out in a timely and effective manner.
Summary: Knowledge is crucial when troubleshooting complex equipment. We hope and need to know all the information related to this issue, including the correct IC revision number, where to find relevant reference materials, and who truly knows what happened at the customer‘s site. IC fault analysis requires fast and accurate response, as of course, helping customers is our main focus. But should we expect the Quality Assurance (QA) department to test every parameter under all conditions during Fault Analysis (FA)? Not at all. Too much of it is speculation. This may surprise some people, but QA personnel do not have crystal balls or mind reading skills. Only when customers provide accurate technical information about IC faults can IC troubleshooting be carried out in a timely and effective manner.
IC Fault Analysis - May Waste Time
We often hear the phrase ‘perception is reality‘. When an IC malfunctions or customers believe it has malfunctioned, we must respond through Fault Analysis (FA). In order to effectively achieve this, we must obtain accurate and relevant information about the event. This is a way to avoid guessing.
Let me tell you about an event that happened not long ago. Some of them were returned due to failure, and we have no knowledge of anything else. We run it on Automatic Test Equipment (ATE) and perform bench testing, X-ray inspection, and cover opening on the parts. We submerged it with soft electrons under an electron microscope to find emission sites indicating damage. We measured its temperature using a liquid crystal coating. This part is perfect. We did not find the cause of the failure, so the QA department accurately stated this in the FA. We would like to know why the parts are considered failed and returned?
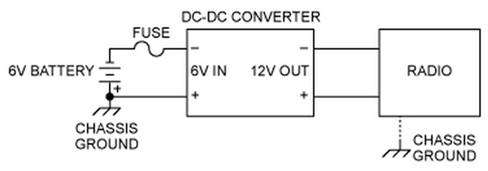
About two months later, we almost accidentally learned that the customer only experienced this fault when the parts were heated to above+60 ° C. We have started FA again. We tested the component at room temperature (+25 ° C) and found... nothing. This component is no longer functional as it was damaged during testing. Ultimately, this is a sexual return activity; It didn‘t happen again. But in this episode, we learned something even more important: without critical performance (i.e. fault) data, we would blindly guess. We wasted a considerable amount of time and money in vain. (For another more personal story about antique cars, grounding issues, and another failed IC, please refer to the IC fault analysis in Appendix - ‘Homefront‘.)
Detailed practice in QA is futile
Many times, the failed IC is severely damaged, making it impossible to determine the root cause of the damage. A customer brought back a circuit board from the assembly contractor to their laboratory facility. They removed the IC from the board there and claimed that the IC had malfunctioned. It‘s very likely. The customer concluded that the ‘root cause‘ lies in the IC itself. They want FA, but where is the fault data? Was the situation carefully recorded at that time? What can prevent future failures? We have returned to speculation, not factual verification - this is hardly a meaningful prescription for FA.
In this case, the customer focuses on the three pins of the multi output device. This is what we know: this part gives the operational certainty of a wafer factory to one in billions; It ran in the circuit for several hours before it failed. Is it a baby malfunction or external processing damage? Is it in the customer‘s circuit? In the application environment? Will electrostatic discharge (ESD) in the factory weaken the circuit, leading to later malfunctions? Perhaps the transport personnel overlooked the damage caused by the ESD protocol? The possible factors seem endless.
The partial schematic received from the customer was not very helpful. It does not display what drives the faulty component, nor does it display what the component needs to drive. The local FAE is required to inspect the ground. Is the ground properly separated? You cannot see from the schematic diagram. We have received more schematic diagrams, but now there are more questions than answers. Why did the customer only check three out of many outputs? Are any input or output pins of the device connected to circuit board pins with low impedance? Are power and grounding considered low impedance connections? May the ESD on the circuit board pins be the problem? We are still guessing.
Effective fault analysis - troubleshooting crime scenes
Now we ask, ‘What can we accomplish with the correct information from the beginning?‘ Expect QA to thoroughly test each parameter under all conditions, especially when we are unaware of the fault? No way. We can only help customers understand the cause of IC failure and can only correct it with a thorough understanding of the application.
Admittedly, this approach conflicts with those who believe that FA should be implemented immediately. I heard that "FA is always something to do. Before checking the application circuit of an IC, you should first check the internal components of the IC." I don‘t understand the origin of this idea, and I also disagree. FA is not the primary task. On the contrary, investigating the ‘crime scene‘, which is a failed event, is a step.
The information on the location of the fault is crucial, just like police investigators, we should do our best to preserve on-site data. Firstly, investigate the application circuit of the IC, i.e. where the fault occurred. Simple questions like solder splatter may be the key to the answer. The IC may partially operate, but it has not completely failed. In fact, removing the IC may mask the real problem.
For an effective FA, we need to check the customer‘s schematic and collect all the situations and reasons for the failure. Yes, this program is likely to encounter customer confidentiality issues. This is a common concern, which is why there are confidentiality agreements (NDAs). This is also the case where FAE acts as the eyes and ears of factories around the world. FAE can enter the customer‘s facility and evaluate the schematic, layout, and other conditions of the application. To protect customer confidentiality, FAE only needs to send the relevant parts of the customer‘s design schematic to QA. Now, quality checks will ultimately use reliable fault data.
Successful results
Back to our story. The local FAE has cooperated more closely with the customer regarding the issue of the malfunction. With more schematic diagrams, here are what we can see. The operational amplifier is connected to the output pin, but due to a 10k Ω series resistor, the impact is not significant. By using a common ground instead of connecting a separate ground at a star point, noise on one power source will be directly coupled to other power sources through decoupling capacitors. The decoupling capacitance of is 0.1 μ F. Typical surface mount 0.1 μ F capacitor self resonates at approximately 15MHz; Above this frequency, they are inductors and no longer act as capacitors.
There are two lessons to be learned. Firstly, decoupling capacitors are bidirectional. If a noisy power supply is coupled to a quiet power supply, noise will contaminate the quiet power supply. Secondly, the same situation can occur with noise grounding: noise can contaminate a quiet power supply. A noisy power supply needs to be paired with a noisy ground, and a clean or quiet power supply must be paired with a clean power supply. Cross contamination can damage power and grounding. Higher than the self resonant frequency of a capacitor, it becomes inductive, meaning it does not conduct or attenuate high-frequency energy.
conclusion
Therefore, we took a detour and repeated the opening line: knowledge is the king when troubleshooting IC faults. From the beginning of the investigation, no one has been more valuable than the local FAE, which checks the issue side by side with the client. FAE must carefully inspect the entire system, circuit board layout, schematic, and application, and then transmit the data back to QA. Only accurate and detailed event data can solve IC fault problems. Without these data, quality inspections would be forced to guess the ‘crime scene‘.
Disclaimer: This article is transferred from other platforms and does not represent the views and positions of this site. If there is any infringement or objection, please contact us to delete it. thank you! |