How to solve the heat dissipation problem of electronic components
Time:2023-07-26
Views:803
Still worrying about the heat dissipation problem of electronic components? This article shares various thermal management solutions and brings effective high thermal conductivity PCB materials to help you solve heat dissipation problems!
With the development of integration technology and microelectronic packaging technology, the total power density of electronic components continues to grow, while the physical dimensions of electronic components and devices gradually tend to be small and miniaturized. The heat generated rapidly accumulates, leading to an increase in the heat flux density around integrated devices. Therefore, high-temperature environments will inevitably affect the performance of electronic components and devices, which requires more efficient thermal control solutions. Therefore, the issue of heat dissipation in electronic components has evolved into a major focus in the current manufacturing of electronic components and equipment.
In response to this situation, engineers have come up with some thermal management strategies: for example, improving heat dissipation capacity by increasing PCB thermal conductivity (high TC); A heat-resistant strategy that focuses on enabling materials and devices to withstand higher operating temperatures (high TD cracking temperature); It is necessary to understand the operating environment and the adaptability of materials to thermal cycling (low CTE). Another strategy is to use materials with higher efficiency, lower power, or lower losses to reduce heat generation.
There are three general ways of heat dissipation, namely: thermal conduction, convection, and radiation heat transfer. So there are several commonly used thermal management methods: when designing circuit boards, intentionally increase the thickness of the heat dissipation copper foil or use a large area of power supply and ground copper foil; Use more thermal conductivity holes; Adopting metal heat dissipation, including heat dissipation plates and locally embedded copper blocks. Alternatively, during assembly, add a heat sink to high-power devices and a fan to the entire machine; Either use thermal conductive materials such as adhesive and grease; Alternatively, heat pipes, steam chamber radiators, high-efficiency radiators, etc. can be used for heat dissipation.
The Shiqiang Intelligent Hardware Innovation Service Platform, launched in 2016, has gathered a complete solution to the cooling problem of electronic components, solved the pain points of enterprise engineers in innovation, and opened up the innovative service chain. More new technologies and solutions related to heat dissipation can be searched and downloaded on the Shiqiang Component E-commerce APP.
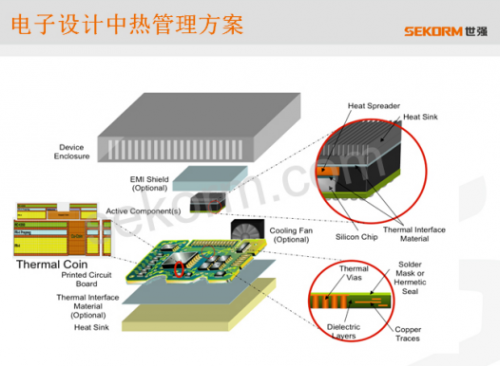
Figure 1: Thermal management solution in the design of Shiqiang Electronics
At present, a new thermal solution has emerged in the market: advocating for the use of high cracking temperature (TD) and high thermal conductivity (TC) plates when designing circuit boards. For example, ROGERS 92ML series laminates currently represented by Shiqiang. As a global leader in high-frequency circuit materials, the Rogers high thermal conductivity PCB material 92 ML series has multiple excellent characteristics, among which the most noteworthy is that the thermal conductivity of 92ML is 4 to 8 times that of standard FR-4 (epoxy resin)!
The characteristics of high thermal conductivity PCB material 92 ML are as follows:
Thermal conductivity (Z-axis) is 2W/M.K (ASTM E1461)
Glass transition temperature Tg: 160 ℃
Pyrolysis temperature Td: 400 ℃ (5%)
Z-axis thermal expansion coefficient (50-260 ℃): 1.8%
UL maximum operating temperature: 150 ℃
The absolute value of pressure resistance of the same medium thickness is higher, with good stability, suitable for high-power and high pressure resistance design requirements
Halogen-free
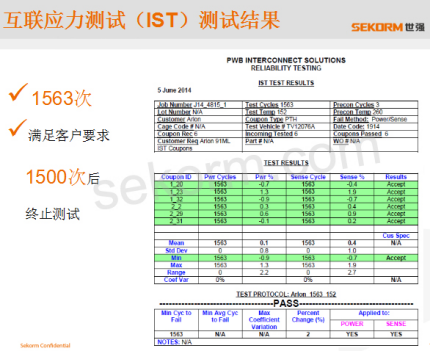
Figure 2: Interconnection Stress Test (IST) Results of 92 ML by Shiqiang Agency
Disclaimer: This article is transferred from other platforms and does not represent the views and positions of this site. If there is any infringement or objection, please contact us to delete it. thank you! |