Countermeasures for Excessive Radiation Emission of Small Power Portable Audio Products
Time:2023-05-09
Views:1032
Low power portable electronic products currently use lithium batteries and Boost (Buck) chips to power devices such as MCU, Audio, and display screens. This type of product usually uses an adapter for power supply, and the design requires that the charging part must pass testing and comply with EMC standards when working. Generally speaking, in order to improve system efficiency, lithium battery charging chips are based on a switch mode of operation, similar to a switching power supply. In addition, other switching power supply chips may work simultaneously, and the devices are all in a switch mode of operation, which improves work efficiency and introduces radiation issues. This is also a common problem in the design process of electronic products. This article provides a detailed analysis of the radiation challenges encountered during the design process based on a product design example (using BQ24133 single battery charging circuit and LM3478 boost circuit). Identify the source of disturbance, identify the coupling path, and ultimately provide a solution for everyone‘s reference.
Introduction to Portable Audio Product Power System
1.1 Background
In actual product development, EMI testing of portable products involves charging the product with an adapter, and connecting other external devices during testing is also necessary. Taking the development of an actual product as an example, this article explains the issues that need to be paid attention to in EMI design of this type of product design, as well as how to analyze the causes of problems when encountering excessive radiation emissions. And find a solution to the problem.
1.2 Audio product power supply circuit
The schematic diagram of the power supply part of an Audio product is shown in Figure 1 below. This product has a charger chip BQ24133, and the maximum charging current is set to 2A in this application. There is a Boost chip LM3478 that boosts the battery voltage to 10V to power the Audio chip, with a full load current of 1A. The other Boost chip LM3478 also boosts the battery voltage to 5V to charge the iPhone or iPad, with a maximum current of 2A. The DC output cable specification of the adapter is 1.5 meters, and the power cable for phone charging is about 0.5 meters. The entire PCB board area is about 12mm × 8mm, designed as a two-layer board.
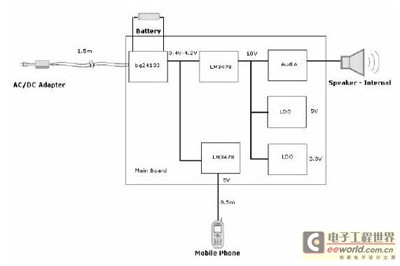
Figure 1: Audio power supply circuit diagram
2. EMI problem analysis
2.1 Generation of EMI issues
This type of portable product requires compliance with standard EN55022, Class B. The initial prototype of this product severely exceeded the radiation emission limit in the frequency range of 30M to 300M during radiation emission testing (without connecting the phone), at around 200MHz, exceeding the limit by over 20DB.
2.2 Analyze the reasons for excessive radiation emissions:
Firstly, analyze the reasons for excessive radiation. We understand the three elements of EMC: disturbance sources, coupling paths, and sensitive devices. The switching devices in this product are undoubtedly disturbance sources, namely BQ24133 (switching frequency 1.6MHZ) and two LM3478 (switching frequency 400KHZ). Looking at the coupling path again, the wavelength corresponding to the 30M to 300M frequency band is from one meter to ten meters. If a certain wavelength of electromagnetic waves needs to be transmitted, a transmitting antenna is required. The necessary condition for becoming an antenna is that the length must be at least one twentieth of the wavelength. When the antenna is an integer multiple of the half wavelength of the electromagnetic wave, the transmission power is maximum. The wires that meet the above conditions to become antennas are a few external wires, most likely the DC power cord and ground wire of the adapter. After analyzing the layout design, it was found that only one ground was used in the product design. The two layers of the entire PCB were extensively paved and connected to the ground wire of the adapter. In addition, the charging wire of the phone formed a ground wire that was more than two meters long. In addition, the BQ24133 charging circuit and the two LM3478 boost circuits are also covered with large areas of ground, causing high-frequency interference to be directly coupled to the ground plane and emitted through a long ground wire.
3. Solution to the problem:
Based on the above analysis, rectification has been made. Due to being a portable audio device without PE cable, Y capacitors cannot be used, and customers do not want to use common mode inductors to increase costs. Therefore, the layout is mainly optimized. The following measures have been taken:
3.1 Layout precautions:
3.1.1) Sort out each power circuit, separate analog ground and digital ground, and do not cross each unit circuit. The digital ground and analog ground of BQ24133 are wired separately and connected to a single point through a 0 ohm resistor under the chip. In addition, the power ground of BQ24133 should be appropriately separated from the ground of the entire product and connected at a single point.
3.1.2) Reduce the area of the harmonic circuit. For LM3478, as shown in the figure, when the MOS transistor is turned on, Cin, L, and MOS form a circuit to charge the inductor. Please refer to Cycle1 in Figure 2 (a). When the MOS transistor is turned off, Cin, L, D, Cout form another circuit to discharge the inductance, as shown in Cycle2 in Figure 2 (b). For diode D, it operates alternately in the forward conduction and reverse cutoff states, so there is a high reverse recovery peak voltage. Snubber circuits need to be added at both ends of the diode to suppress this peak voltage to avoid generating excessive common mode noise. The working frequency of these two circuits is the switching frequency of MOS, and the harmonic component is large. When arranging the board, it is necessary to minimize the area of the harmonic circuit as much as possible. To place the components of these two power circuits close together, use a wide copper wire to reduce the circuit impedance of switching frequency harmonics.
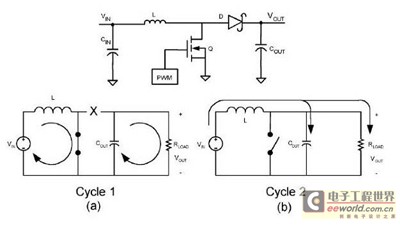
Figure 2: LM3478 working principle diagram
BQ24133 is essentially a Buck circuit. There are also similar issues. Please refer to Figure 3, the working principle diagram of BQ24133. The input capacitor C1, the rectifier tube on, the freewheeling tube off, the rectifier tube inductance and load form a high-frequency circuit, with a high dI/dT. In addition, when the rectifier is turned off and opened, the inductor current continues to flow through the coil (which operates in the continuous inductor current mode during heavy loads). When the inductor current does not decrease to zero, the rectifier will open again. This is because the coil is forced to apply a reverse voltage and cut off, resulting in a high reverse recovery voltage peak (although synchronous rectification, due to the existence of a dead time, diode rectification is still used during the dead time), This will result in relatively large common mode noise, so it is necessary to add a Snubber circuit in SW to PGND to suppress the reverse spike of the freewheeling tube. Therefore, the input filtering capacitor C1, inductor L1, and output filtering capacitor C2 should be arranged as close as possible to the chip to reduce the high-frequency circuit area. The power circuit wiring should be routed with a large copper sheet width to reduce harmonic impedance, preferably arranged on the same layer as the PCB, with the Snubber placed close to the lower tube.
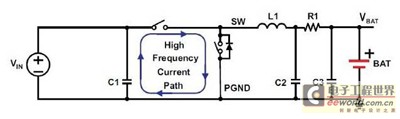
Figure 3: BQ24133 High frequency current circuit diagram
Overall, the input and output of LM3478 and BQ24133 run through a large copper sheet, placing the input and output capacitors close to the power switch transistor to minimize the area enclosed by the circuit. The capacitor with smaller ESR is selected. Because of the cost, the capacitor used in this kind of products is relatively poor. This project used to use electrolytic capacitor, and it is recommended to add more ceramic chip capacitors for combination use, so as to achieve good results at low cost. In this way, the harmonic circuit of the input and output switching frequency is minimized, and the harmonic impedance is minimized, which can reduce the external radiation interference of the circuit.
3) As mentioned above, a Snubber circuit is added to the lower transistor of BQ24133 (between SW and PGND), and a Snubber circuit is added to the freewheeling diode of LM3478. The Snubber circuit adheres closely to the switch pin, widens the wiring, and bypasses high-frequency harmonics nearby. Firstly, a 2-3ohm resistor can be pre placed, with a capacitance of 500-1000pF. In radiation testing, if the margin is insufficient or exceeds the specification, RC should be appropriately increased to absorb more high-frequency energy. If the margin is too large, the value of RC should be reduced to improve efficiency.
4) For two-layer boards, remove or reduce the GND copper skin below the wiring between power devices such as inductors and MOS and power devices. Reduce the distributed capacitance of the switch tube to GND and reduce common mode coupling.
3.2 Other precautions
3.2.1 Layout
Generally speaking, if conditions permit, the power circuit should be appropriately separated from other circuits in layout as much as possible. For example, place power devices on the left side of the PCB and leave appropriate isolation strips with other circuits. Try to keep the output line and terminals away from switches, inductors, and other devices as much as possible. On circuits with high harmonics, pay attention to avoiding sharp corners in PCB wiring, and try to chamfer obtuse corners or rounded corners.
3.2.2 Use of common mode inductors
For multiple batteries, with an increase in charging power, the length of the battery output line should be minimized as much as possible to avoid the battery line becoming a radiation antenna. In addition, it can be considered to increase the common mode inductance appropriately to suppress the common mode interference of the battery line.
3.2.3 Test precautions
It is recommended that customers use a battery and a 1.5 meter cable as the input source during radiation testing to eliminate interference caused by the adapter. In addition, the Snubber parameter is adjusted during the test to achieve a balance between efficiency and EMI. The RC value cannot be increased too much to avoid overheating the IC. Therefore, when the interference source noise is relatively high, it is necessary to consider using multiple measures simultaneously to achieve the optimal effect.
4. Conclusion:
After rectification, the layout was optimized and successfully passed the radiation test. Summarize some experience from this project. Firstly, determine the disturbance source and transmitting antenna, and increase the Snubber circuit to absorb high-frequency harmonics from the disturbance source. Secondly, determine the coupling path, with a focus on optimizing the layout to allow harmonics to pass through nearby capacitor bypasses, reducing the coupling of high-frequency disturbances from disturbance sources to external long lines. The essence of EMC design is how to handle harmonic issues well.
Disclaimer: This article is transferred from other platforms and does not represent the views and positions of this site. If there is any infringement or objection, please contact us to delete it. thank you! |