Three Ways for MCU to Solve Common Design Challenges of Traction Inverter for 800V Electric Vehicle
Time:2023-01-16
Views:1404
Electric vehicle (EV) traction inverter is electric vehicle. It converts the DC of high-voltage battery into multi-phase (usually three-phase) AC to drive the traction motor and control the energy regeneration generated by braking. Electric vehicle electronic products are changing from 400V to 800V architecture, which is expected to achieve:
·Fast charging – double the power at the same current.
·Improve efficiency and power density by using silicon carbide (SiC).
·Reduce the current required for 800V voltage at the same rated power by using thinner cables, thus reducing weight.
In the traction inverter, the microcontroller (MCU) is the brain of the system. The motor control, voltage and current sampling are carried out through the analog-to-digital converter (ADC), the magnetic core is used to calculate the field-oriented control (FOC) algorithm, and the pulse width modulation (PWM) signal is used to drive the power field effect transistor (FET). For MCU, the transformation to 800V traction inverter brings three challenges:
·Real-time control performance requirements with lower latency.
·Added functional safety requirements.
·Need to respond quickly to system failure.
In this article, we will discuss how to meet these challenges with devices such as the Arm-based SitaraAM2634-Q1 and C2000 MCU.
In this article, we will discuss how to meet these challenges with devices such as the Arm-based SitaraAM2634-Q1 and C2000 MCU.
Real-time control with lower latency
In order to control the torque and speed of traction motor, MCU uses the combination of peripheral devices (ADC, PWM) and computing core to complete the control loop. With the switch to 800V system, traction inverters also turn to broadband gap semiconductors (such as SiC), because they greatly improve efficiency and power density at 800V. In order to achieve the higher switching frequency required by SiC, this control loop delay becomes a priority. The low delay control loop also enables engineers to run the motor at a higher speed, thus reducing the size and weight of the motor. To understand and shorten the control loop delay, you must understand the control loop signal chain and its various stages, as shown in Figure 1.
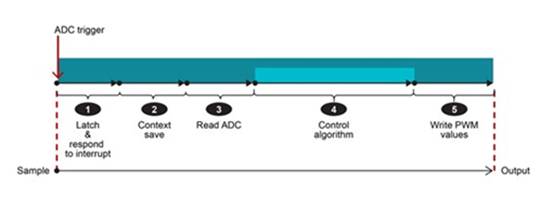
Figure 1: Control loop signal chain
To achieve excellent real-time control performance, you must optimize the entire signal chain, including hardware and software. The time spent from ADC sampling (input from the motor) to writing PWM (output to control the motor) is the basic measure of real-time control performance. Starting from ADC sampling, the inverter system needs accurate and fast sampling, that is, to achieve high sampling rate, at least 12 bit resolution and low conversion time. Once it can be sampled, it needs to be transmitted to the processor and read by the processor through interconnection, and the optimized bus and memory access architecture reduces latency. In the processor, the kernel needs to use FOC algorithm to calculate the next PWM step according to the phase current, speed and position of the motor.
In order to reduce computing time to a greater extent, the kernel needs a higher clock rate and must efficiently execute a specific number of instructions. In addition, the kernel needs to execute a series of instruction types, including floating-point, trigonometric, and integer math instructions., The kernel uses the low latency path again to write the updated duty cycle to the PWM generator. Applying dead-time compensation on PWM output will prevent short circuit when switching high side and low side FETs, and apply it at hardware level to reduce software overhead.
The delay of traction inverter control loop of TI MCU is as low as 2.5s, and the delay of AM2634-Q1 is less than 4s. This level of control loop delay will be targeted at future designs including SiC architecture,.
Add functional safety requirements
Since traction inverters provide power to control motors, they are essentially functional safety critical systems. Because the 800V system is likely to provide higher power, torque, speed (or both), the traction system needs to meet the requirements of ASIL Level D for functional safety. A key part of the functional safety system is the MCU, because it needs to make intelligent decisions to respond to system failures. Therefore, the use of MCU through ASIL D is an important security element.
In order to make engineers more easily meet the system safety requirements specific to traction inverter, TI MCU provides additional functions. For example, phase current feedback represents information about motor torque, which makes these signals critical to safety. Therefore, many engineers prefer redundant sampling of phase current, which means that the MCU must have multiple independent ADCs.
Quick response system failure
Another challenge for engineers is to quickly put the motor in a safe state in case of failure, such as continuous current. In the AM2634-Q1 device, the fault universal input (for overcurrent, overvoltage or high-speed fault) will enter the innovative programmable real-time unit (PRU). The firmware implemented in the PRU can correctly evaluate and respond to the fault type and execute the required PWM protection sequence, as shown in Figure 2, and then directly put the PWM in the safe state as required. These operations take place in just 105 ns. In addition, because the firmware is user programmable, engineers can add additional custom logic to meet their application requirements when necessary.
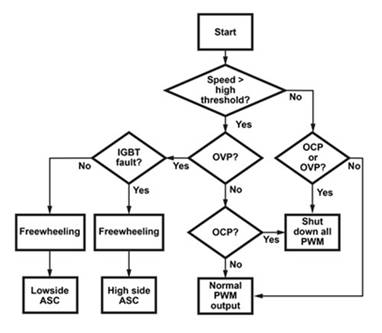
Figure 2: Flow chart shows the expected protection behavior of PWM output based on fault input
With the production of more and more electric vehicles, the design trend will turn to SiC and 800V technology. At the same time, it is necessary to improve the motor control performance and meet the functional safety requirements of traction inverter. With the development of the world towards electrification, innovation in performance and efficiency is crucial to help automotive engineers design the next generation of electric vehicles.
Disclaimer: This article is transferred from other platforms and does not represent the views and positions of this site. If there is any infringement or objection, please contact us to delete it. thank you! |