DC motor controller: Brushed and brushless
Time:2022-11-26
Views:1551
Author: Andrey Solovev
DC motor controller is a special electronic device used to manage the operation of DC motor. Do all DC motors need controllers? Not at all. Let‘s figure out which DC motors use it and for what purpose.
In this paper, we will study two types of DC motors: Brushed DC (BDC) and Brushless DC (BLDC) motors. Both types use controllers to start and stop the motor, regulate its speed and torque, and perform other functions. However, the controller is more important for BLDC motors because it is part of the commutation process and is critical for all motors powered by DC. Here, you will learn more about the differences between brushless and brushless DC motors and their control systems.
Overview of BDC and BLDC motors and controllers
To create the rotation of a DC motor, you need to switch or reverse the current applied to the motor and change the polarity of the magnetic field generated around the motor winding components.
In BDC motors, the current flows through the winding of the rotor, and its stator can have windings (series, parallel, composite BDC motors) or permanent magnets (permanent magnet BDC motors). The movement of the motor depends on the interaction of the magnetic fields generated around these two components. Therefore, their fields with opposite charges attract and similar electric fields repel each other.
Another key component of BDC motor is commutator, which switches the polarity of current and applies it to the rotor winding through the electric contact point called brush.
BLDC motors also have a rotor and a stator, but unlike brushless motors, the current flows through the stator windings. The rotor made of permanent magnet can be located inside the motor (inner rotor BLDC motor) or outside (outer rotor BLDC motor).
BLDC motor has no mechanical components such as commutator or brush, because the commutation here is an electronic process driven by the controller. By estimating the position of the rotor, the controller decides when to switch the current and which stator winding is energized. Therefore, the controller is very important for the operation of brushless motor.
In addition, BDC and BLDC motor controllers have the same functions; They can start and brake the motor, reverse its rotation and control its speed and torque.
Application Characteristics of Brushed and Brushless DC Motors
Brushed and brushless DC motors have their own advantages and disadvantages, and their application fields are defined. For example, BLDC motors have smaller, lighter structures that have no effect on their efficiency. This is why it is widely used in portable electronic products and wireless devices of different sizes.
Compared with mechanical commutator, BLDC motor controller switches current at a higher frequency. This allows the motor to maintain high torque and operate smoothly at low and high speeds. Reliability and low maintenance are also the strengths of BLDC motors. Therefore, its scope of application may include its use in the following aspects:
Electric vehicle;
Unmanned aerial vehicle;
Household electronic products;
Industrial robot.
In some applications, BDC motors have given way to brushless motors. In fact, the mechanical commutation efficiency is low, which usually leads to power loss. Sparks generated during current switching can cause high levels of electronic noise. In addition, brushes require regular maintenance and/or replacement.
Despite all these shortcomings, BDC motors are still popular in low-power systems and applications that focus on simplicity and cost-effectiveness. They can be found in remote control toys, simple household, industrial and automotive appliances.
The design and implementation of BDC motor controller is simpler than BLDC controller, because there are no complex electronic components and algorithms, which makes it a more attractive choice in some cases. So let‘s look at what it takes to build each of these devices.
Build BDC motor controller
Before constructing the DC motor controller, the technical requirements shall be specified and the specific type of equipment shall be selected. The characteristics of the controller include but are not limited to:
Power regulation
To adjust speed or torque, the BDC controller increases or decreases the power supplied to the motor. The linear regulator allows the controller to apply a constant voltage throughout the motor‘s duty cycle.
This type of regulation is usually no longer used in modern controllers because they rely mainly on switching regulators with pulse width modulation (PWM). This method allows the controller to change the voltage and current levels through pulsed power supply.
control type
A simple system uses a DC motor controller to adjust the operation of the motor without any feedback. Therefore, the open-loop controller cannot correct the motor parameters.
In contrast, the closed-loop DC motor controller can receive feedback from the motor and adjust its speed, rotation direction and other parameters as required.
Other characteristics of the DC motor controller include the power and operating voltage of the motor. To ensure the reliability of the motor and its controller, you should know the power supply and voltage level required for normal operation of the motor. Therefore, you can choose between low-voltage and high-voltage and power motor controllers.
As mentioned above, most brushless motors use PWM controllers. Such devices have an H-bridge circuit with two high side and two low side switches. For example, when the motor needs to accelerate, the controller will increase the duty cycle (the ratio of pulse to pulse period). The modified PWM signal reaches the gate drivers, which turn on the transistors for a longer time and allow more current to enter.
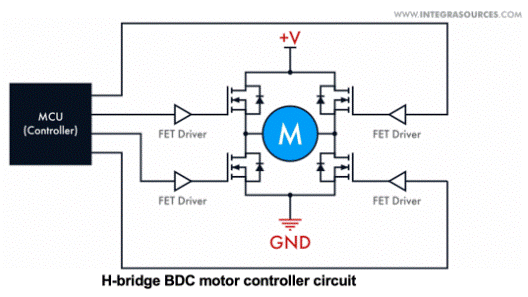
To rotate the BDC motor in one direction, the controller turns on the H-bridge switch on the diagonal. There is always some delay in the switching process, so when the rotation is reversed, all four transistors may turn on. To prevent voltage and current leakage from the motor, you can increase the dead time so that the controller keeps all transistors closed and on in turn.
To achieve a closed loop control circuit, a position sensor can be used. The controller will read the signal sent by the sensor and make corresponding response. In one of our projects, we created a programmable DC motor controller, which can work as both a closed loop system and an open loop system. In order to receive feedback from the motor, we added a rotary encoder to monitor the condition of the motor.
When building a DC motor controller with feedback, you should pay attention to the function of the microcontroller. MCU shall:
Covering the frequency range of sensor signal;
Necessary signal processing rate;
Sufficient memory and flash memory capacity;
If the sensor is an analog sensor, it has an analog to digital converter (ADC).
Building BLDC motor controller
The BLDC motor controller uses transistors in a half H-bridge circuit to switch current. The number of transistors depends on the number of phases or windings excited by the controller. Three phase brushless DC motor controller (one of the most common configurations) requires three and a half H-bridges, that is, one high side switch and one low side switch per phase.
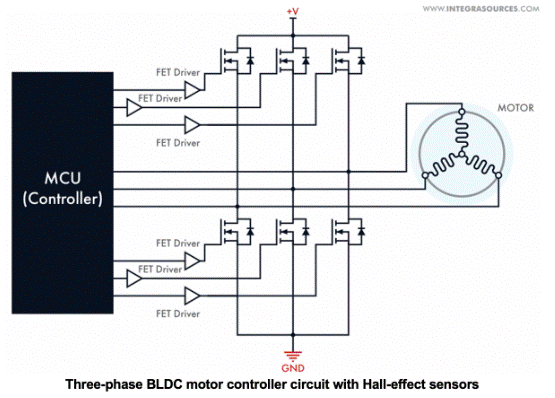
After receiving the MCU signal, the gate driver turns on the transistors and supplies current to the stator windings. To switch between phases, the controller needs to know the position of the rotor. There are two ways to detect it:
Install the position sensor and use its measured value;
Sensing the back electromotive force (back electromotive force) generated with the rotor movement in the stator winding.
The first method is simpler, but the sensor requires regular maintenance (for example, optical sensors are prone to dust). In addition, you must add more wires, which complicates the structure of the motor. The second solution is simpler at the hardware level, but may require complex algorithm development. It is important that you can sense the return EMF only when the rotor is moving.
According to our experience, when the sensor is used together with the back EMF sensing method, the positioning accuracy will be improved.
When the rotor position is detected, the BLDC motor controller switches the current and applies it to different phases as a trapezoid or sine wave.
The realization of trapezoidal commutation is simpler, but it may cause torque ripple at low speed and become stable only when the motor accelerates. Sinusoidal DC brushless motor controller mainly relies on pulse width modulation to generate sine wave. This method can provide smooth switching at low speeds, but it is difficult to build a sine wave at high frequencies.
Most brushless motors have closed loop controllers that use position sensors and special algorithms to receive feedback from the motor and respond. One of the algorithms is proportional integral derivative (PID) algorithm, which is widely used in BLDC and BDC motor controller feedback systems.
PID algorithm processes current motor parameters and compares them with reference values. Based on these data, it adjusts the frequency of the output signal, and the controller adjusts the speed accordingly.
conclusion
DC motor is in great demand in various industries. It is interchangeable in some applications, and BDC and BLDC motors still have their niche markets. For example, the low cost and simplicity of the brush motor make it a suitable choice for electronic equipment in daily use. The electronic commutated BLDC motor can provide reliable and efficient speed control in different power applications.
Disclaimer: This article is transferred from other platforms and does not represent the views and positions of this site. If there is any infringement or objection, please contact us to delete it. thank you! |