Integrated brush DC solution how to reduce the size of automotive motor, enhance protection and simplify design
Time:2022-07-03
Views:2031
With simple control, low cost and diverse functions, brushless DC motor is very suitable for automotive loads that need integrated high-power and reliable motor drivers, such as window lifters, sunroof controls, door locks, latches and engine valves.
If you are designing an automotive system, you may face both device level and system level challenges, including size constraints, failure conditions, and the need to meet the requirements of reusability to shorten development time. Therefore, this article will analyze these challenges in detail and provide corresponding solutions.
Using fully integrated high power density motor driver to reduce the size of the system
When designing a cost optimized automobile system, we should focus on reducing the size of the system and saving the space of the layout. Reducing the package size and integrating functions into the brushless DC drive can reduce the number of external components, thereby saving board space and reducing costs.
When designing a small system, the following improvement methods should be considered:
Small package size - for high power density solutions, use a small package size with high current capability. Drv8243-q1 series has launched automotive hotrod tetragonal flat leadless package, with a size lower limit of 3mm x 4.5mm. It is one of the ultra small packages used for brushless DC drives in similar products.
Integrated current detection - with internal current regulation and current feedback pins, there is no need for external current detection resistors, thereby saving board space and reducing costs.
Integrated field effect transistor (FET) solution - drv8243-q1 series can drive up to 32A H-bridge peak current and 46a half bridge peak current. With an integrated solution supporting medium and high current, there is no need to use grid drivers and external FETs, which can save board space and reduce costs. The current capacity depends on the printed circuit board design and ambient thermal conditions, so be sure to check our transient thermal calculator to understand the current value that your system can drive.
Using smaller packages (as shown in Figure 1) and minimizing the number of external components can reduce the size of the circuit board and reduce the bill of materials cost.
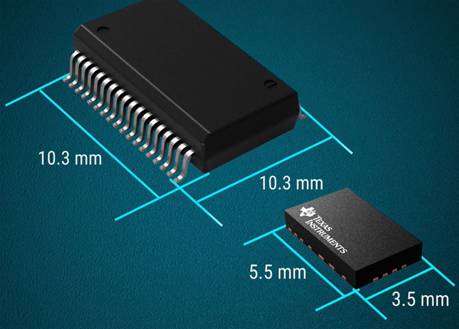
Figure 1: drv8245-q1 device series size comparison
Protection and diagnostic capabilities of reliable solutions
Motor drivers play an important role in various applications, from electric trunk doors to gas engine valves. Therefore, it is necessary to design a reliable solution that can detect and prevent various fault conditions.
Drv8243-q1 device series is the first device that can provide open circuit load detection and short circuit protection when the motor driver is in the on and off state. Figure 2 shows how the device offline protection function uses a passive resistor network connected to the H-bridge to detect system problems before enabling the FET. Even if the H-bridge is off, this function helps to avoid damage or abnormal behavior of the motor driver.
Figure 2: closed state diagnosis of drv8243-q1
Off line diagnosis is helpful to protect the motor driver from faults in other parts of the system and avoid overall wear. For more information about how ti offline protection function protects the automotive system, please refer to the application manual "open circuit load detection in motor driver"
The serial peripheral interface option provides detailed diagnosis to confirm the type and location of faults. By providing the root cause of motor driver faults, designers can save time to solve problems.
Optimized design with scalable drives
The motor driver drives various loads in the car, such as relays, solenoid valves and motors. Sometimes, these loads are all collected in the same application, such as door module or body control module.
The H-bridge and half bridge drives of drv8243-q1 series support design reuse and can expand different loads in automotive systems. The device series has similar firmware, functions and package pin arrangement, and supports reuse in various load and current ranges, which helps to shorten the design time. When used in independent mode, the H-bridge driver can drive two one-way brush DC motors, solenoid valves or relays without two independent half bridge drivers; As shown in Figure 3.
Figure 3: drv8243-q1 series models are used to realize the expansion across multiple loads
In addition to having similar firmware, drv8243-q1 and drv8244-q1 lead-in packages are also pin to pin compatible, so it is easier to insert and replace these devices when the power level is scaled up or down.
When designing automotive solutions, solution size, protection performance and design reuse are key factors to be considered. If you have any questions about the relevant contents in this article, you are welcome to raise them in the Ti E2E motor driver forum.
If you are designing an automotive system, you may face both device level and system level challenges, including size constraints, failure conditions, and the need to meet the requirements of reusability to shorten development time. Therefore, this article will analyze these challenges in detail and provide corresponding solutions.
Using fully integrated high power density motor driver to reduce the size of the system
When designing a cost optimized automobile system, we should focus on reducing the size of the system and saving the space of the layout. Reducing the package size and integrating functions into the brushless DC drive can reduce the number of external components, thereby saving board space and reducing costs.
When designing a small system, the following improvement methods should be considered:
Small package size - for high power density solutions, use a small package size with high current capability. Drv8243-q1 series has launched automotive hotrod tetragonal flat leadless package, with a size lower limit of 3mm x 4.5mm. It is one of the ultra small packages used for brushless DC drives in similar products.
Integrated current detection - with internal current regulation and current feedback pins, there is no need for external current detection resistors, thereby saving board space and reducing costs.
Integrated field effect transistor (FET) solution - drv8243-q1 series can drive up to 32A H-bridge peak current and 46a half bridge peak current. With an integrated solution supporting medium and high current, there is no need to use grid drivers and external FETs, which can save board space and reduce costs. The current capacity depends on the printed circuit board design and ambient thermal conditions, so be sure to check our transient thermal calculator to understand the current value that your system can drive.
Using smaller packages (as shown in Figure 1) and minimizing the number of external components can reduce the size of the circuit board and reduce the bill of materials cost.
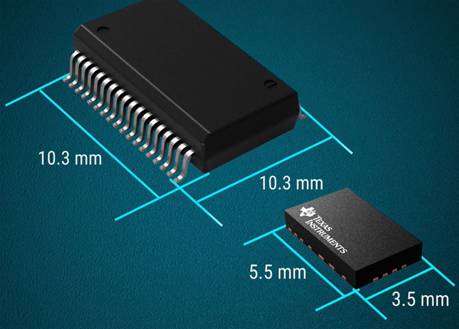
Figure 1: drv8245-q1 device series size comparison
Protection and diagnostic capabilities of reliable solutions
Motor drivers play an important role in various applications, from electric trunk doors to gas engine valves. Therefore, it is necessary to design a reliable solution that can detect and prevent various fault conditions.
Drv8243-q1 device series is the first device that can provide open circuit load detection and short circuit protection when the motor driver is in the on and off state. Figure 2 shows how the device offline protection function uses a passive resistor network connected to the H-bridge to detect system problems before enabling the FET. Even if the H-bridge is off, this function helps to avoid damage or abnormal behavior of the motor driver.
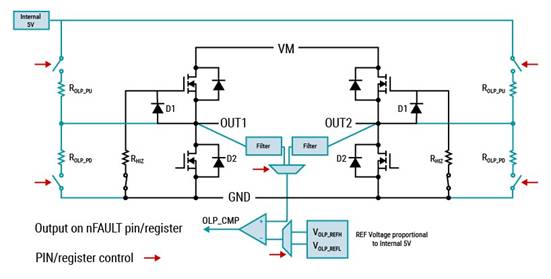
Figure 2: closed state diagnosis of drv8243-q1
Off line diagnosis is helpful to protect the motor driver from faults in other parts of the system and avoid overall wear. For more information about how ti offline protection function protects the automotive system, please refer to the application manual "open circuit load detection in motor driver"
The serial peripheral interface option provides detailed diagnosis to confirm the type and location of faults. By providing the root cause of motor driver faults, designers can save time to solve problems.
Optimized design with scalable drives
The motor driver drives various loads in the car, such as relays, solenoid valves and motors. Sometimes, these loads are all collected in the same application, such as door module or body control module.
The H-bridge and half bridge drives of drv8243-q1 series support design reuse and can expand different loads in automotive systems. The device series has similar firmware, functions and package pin arrangement, and supports reuse in various load and current ranges, which helps to shorten the design time. When used in independent mode, the H-bridge driver can drive two one-way brush DC motors, solenoid valves or relays without two independent half bridge drivers; As shown in Figure 3.
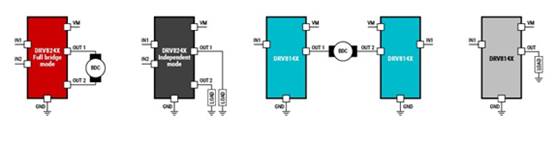
Figure 3: drv8243-q1 series models are used to realize the expansion across multiple loads
In addition to having similar firmware, drv8243-q1 and drv8244-q1 lead-in packages are also pin to pin compatible, so it is easier to insert and replace these devices when the power level is scaled up or down.
When designing automotive solutions, solution size, protection performance and design reuse are key factors to be considered. If you have any questions about the relevant contents in this article, you are welcome to raise them in the Ti E2E motor driver forum.
Disclaimer: This article is transferred from other platforms and does not represent the views and positions of this site. If there is infringement or objection, please contact us to delete. thank you! |